Box Conveyor Integration
Company: Walzcraft – Cabinet Door and component supplier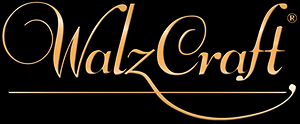
Project Scope:
Walzcraft employed Industrial Automation and Engineering to design and integrate an industrial control system to an existing conveyor system. The control system was to automate a roller conveyor that will start, stop, accumulate, and apply brakes based on the current position and quantity of the boxes on the roller conveyor.
Previous Method:
The existing conveyor came with motors and line shafts, a lift gate, and two motor starter panels. None of this equipment was commissioned because there was no industrial control for the entire system. An operator would put finished parts into boxes and then proceed to push the boxes down the conveyor. The conveyor was roughly 300 feet long so the boxes would make it about half way down the conveyor until they would come to a stop. At that point, the operator at the other end of the conveyor would then walk halfway up the conveyor to retrieve the box and push it down to the end where the same operator would then finish the boxing process.
Not only was this not time efficient, but created unnecessary extra wear and tear on the operators that left them fatigued at the end of the shift.
Project Integration and Design:
Industrial Automation worked with Walzcraft to not only integrate the motor controls, industrial control panel, and sensors for conveyor functionality, but also to yield improved efficiency, operator friendliness, and safety. In order to accomplish this, Industrial Automation provided a separate control panel that would house a Click PLC, a C-More Micro EA3 series touch screen, and other control components and terminations. Industrial Automation developed a PLC program that would monitor the sensors and control the conveyor braking system and motor starters. We also developed a touch screen program that would allow the operators to manipulate timers such as how long a sensor reads a box before applying the brake(s), automatic shutdown if the conveyor was not being used, and start/stop delays.
Industrial Automation was able to make the system work as follows: The operator at the beginning of the conveyor would push the box down the conveyor from his current position. The box would then be sensed by the start of the line sensor. When sensed, the motor starters would turn on and start the conveyor. There were also start/stop buttons on each motor starter, control panel, and on the touch screen that could also start/stop the conveyor at each location. Once the box reached the end of the conveyor, it would be sensed and apply a brake to only that accumulation zone of the conveyor causing the box to halt. As another box followed, it would be sensed and would apply the brake to the next upstream accumulation zone of the conveyor causing the box to stop before reaching the first box. There were 5 accumulation zones, all at the end of the conveyor, that were manipulated this way. This was to prevent the boxes stacking up at the end of the conveyor. Once the first box was taken off the conveyor, the brakes would release and allow the boxes to move one accumulation zone closer to the end. After the five zones were occupied, the boxes were allowed to stack up. When there were so many boxes stacked up, a “line full” sensor would turn the downstream conveyor off, not allowing the stack to overload. A proximity sensor was installed at a lift gate half way down the conveyor to stop the upstream conveyor if the gate was opened. A sensor was installed near a column to shut down the downstream conveyor if the column was to come in contact with a box moving on the conveyor. The Powerflex4 VFD’s in motor control panels were re-programmed to integrate with the new control system and programming.
Results:
This integration project has provided a much more user friendly conveyor system, reduced operator fatigue, decreased wasted time, increased output, and has allowed the operators to control the conveyor in multiple different ways.