IO Link Plant Visibility
Customer: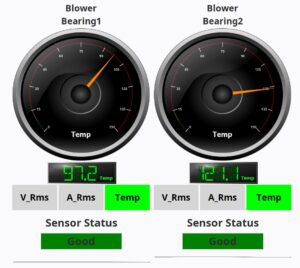
Torrance Casting
Scope:
Traditionally, a PM schedule was utilized to maintain machinery, however when equipment develops an issue and is not monitored or in sight of maintenance staff, the problem is unnoticed causing unscheduled production downtime.
This foundry has a lot of machinery in a very dirty environment. A well informed maintenance staff and machine visibility is critical to keep machinery running and at peak performance. Motor bearing health was one of areas where Torrance casting wanted real time visibility, trending, and alarming.
Design:
The foundry’s SCADA system is built on the Ignition platform, by Inductive Automation. IFM’s vibration sensors with IO Link communications and IO Link Master blocks with MQTT & JSON ports were specified for this application. The vibration sensors were mounted to the bearing housing using magnet mounts. Each sensor was routed back to one of the IO Link Master blocks 8 ports. The block was powered externally and the MQTT/ JSON port was connected to the plant control network. Ignition’s UDT’s were created with embedded python scripting to request data from each of the connected sensors. In addition to required v-RMS data, each vibration sensor also delivers a-RMS, a-Peak, Crest, Temperature, and device status. Each sensor’s data is displayed real time, historically trended, and monitored for out of tolerance vibration and temperature levels. Alarms can be configured to notify maintenance staff of any out of tolerance readings.
Results:
Torrance Castings maintenance staff now has “eyes on” out of sight equipment. The real time and historical data trending allows them to see current status, create baselines, and to develop PM schedules for each of the bearing sensor locations. Warning & Alarm level notifications are configured based on these baselines to alert staff in the event that a bearing is failing before scheduled maintenance.